2.1 一般要求
2.1.1 构成EGC 系统的机械设备、电气设备及控制系统等,应分别按CCS《钢规》第3、4、7 篇规定的环境条件/工作环境进行设计、选型、布置。
2.1.2 EGC 系统相关管系、设备的材料应与其接触介质的特性及工作条件相适应。
金属和非金属材料选择时一般应遵循如下原则:
(1) 金属材料宜以碳钢材料为主。对金属材料表面可能接触腐蚀性介质的区域,应根据脱硫工艺不同部位的实际情况,衬以抗腐蚀性和耐磨损性的非金属材料;
(2) 当以金属材料作为承压部件,所衬非金属材料作为防腐部件时,应充分考虑非金属材料和金属材料之间的黏结强度,同时,承压部件的自身设计应确保非金属材料能够长期稳定地附着在承压部件上。
(3) 对于接触腐蚀性介质的某些部位,如果采用碳钢衬以非金属材料难以达到工程 应用要求,应根据介质的腐蚀性和磨损性,采用以镍基材料为主的不锈钢。当经过充分论证后,部分区域也可采用具有抗腐蚀性的低合金钢。其适用介质条件见表2-1。
表2-1 镍基不锈钢适用介质条件
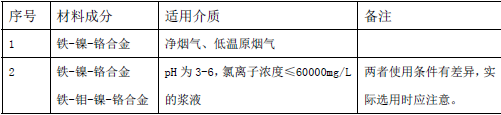
(4) 非金属材料主要可选用玻璃鳞片树脂、玻璃钢、塑料、橡胶、陶瓷类产品用于防腐蚀和磨损,其适宜的使用部位见表2-2。对于含氟较高的烟气,防腐材料中不得含有玻璃成分。
表2-2 主要非金属材料及使用部位
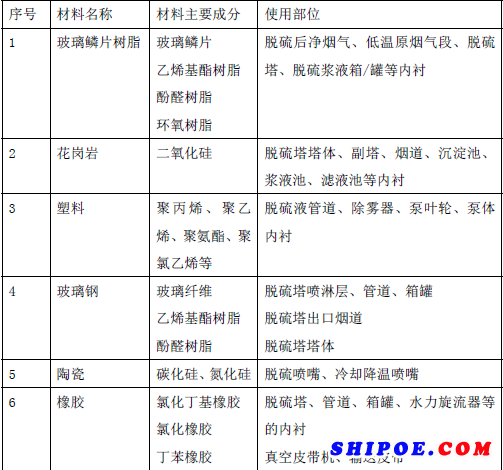
2.1.3 可能积聚可燃、有毒或蒸汽的处所,应满足第3 篇1.3.4 的通风要求。
2.1.4 暴露于腐蚀环境的零部件及管系,应满足第3 篇1.3.5 的防腐蚀要求。
2.1.5 应按《钢规》第3 篇第1 章1.3.6 的要求设有适当的防护措施,防止EGC系统工作和维护时可能对船上人员造成的伤害。
2.1.6 EGC 系统对船舶稳性和载重线的影响应进行评估,评估时需考虑EGC 系统工作状态,计算与评估有关的详细资料应提交船级社批准。
2.1.7 EGC 系统应能在热态工况下投入工作,不会由于热冲击造成任何破坏。
2.1.8 如系统运行时可能出现烟灰沉积、结垢等,应考虑采取适当的措施予以清理。
2.1.9 EGC 系统的安装及运行应不会导致柴油机的NOx 排放超出柴油机EIAPP 证书中的规定值。
2.1.10 EGC 系统的结构设计、布置应便于安装、操作和维护。
2.1.11 如废气系统除安装EGC 系统以外,还安装了其他后处理装置(如SCR),则船上安装时应考虑这些后处理系统之间的兼容性。
2.2 与燃油燃烧设备匹配
2.2.1 每一拟安装的EGC 系统,应能有效地处理与其相连燃油燃烧装置最大持续功率(MCR)工况下的废气排放。对于柴油机,MCR 是指其额定功率,对于锅炉,是指额定蒸发量或额定热功率。
2.2.2 对于EGC 系统与多台燃油燃烧装置相连的情况,如实际营运时并非所有与之相连的燃油燃烧装置同时工作,EGC 系统的废气处理能力可按实际工作时最大可能的废气排放量之和确定,而不必考虑所有装置同时运行工况。
2.2.3 各种工况及运行模式下,EGC 系统应与所连接燃油燃烧装置匹配,相关资料应提交船级社批准。
2.3 排气背压
2.3.1 EGC 系统船上安装后,在各种运行条件下排气背压应能始终维持在燃油燃烧装置制造厂规定的范围内。
2.3.2 如需安装风机以维持所需背压,风机的设置应考虑当其失效时,燃油燃烧装置仍能持续工作。对于多台燃油燃烧装置共用EGC 系统的情况,风机的设置应考虑所有相连燃油燃烧装置的背压要求。
2.3.3 应采取合适的措施减少风机(如设有)因腐蚀、脏堵而影响其正常工作的风险。
2.4 旁通或其他等效措施
2.4.1 EGC 系统的设计与布置应保证当EGC 系统故障或正常停止工作时,燃油燃烧装置仍能正常运行。
2.4.2 如设有旁通装置,应设有正确指示其工作状态的装置。旁通装置应工作可靠,任何情况下应保证燃油燃烧装置能安全运行。
2.4.3 如不设旁通,应确保即使EGC 系统停止工作,燃油燃烧装置产生的高温排气也能顺利排出,而不会对EGC 系统及其构件造成破坏。这种情况下,EGC 系统的设计还应考虑高温排气直接冲刷后灰尘积聚、结碳等风险。
2.5 排气管互连
2.5.1 一般情况下,船上各个燃油燃烧装置的排气管应相互独立,不允许相互连接。如设计者充分考虑了潜在风险,并采取有效隔离装置防止排气倒流至停止工作的燃油燃烧装置,经本社同意,允许多个燃油燃烧装置的排气管连接至同一EGC 系统进行排气处理。
2.5.2 应采取有效措施,防止隔离装置处于关闭状态时起动被隔离的燃油燃烧装置。
2.5.3 隔离装置应工作可靠,任何情况下发生故障,应保证燃油燃烧装置能安全运行。
2.6 脱硫剂选用及其贮运
2.6.1 选用氧化镁(MgO)作脱硫剂时,氧化镁含量宜大于85%或者满足EGC 系统制造厂的规定,酸不溶物宜小于3%(干基)。
2.6.2 脱硫剂的贮运、制备系统应设有必要的扬尘污染控制措施。
2.6.3 当采用粉状脱硫剂时,物料装卸区的布置应考虑风向。
2.6.4 应采取必要的措施防止脱硫剂贮存时吸潮、变质与板结。
2.6.5 脱硫剂储存舱/柜的容量设计,应考虑船舶拟营运的航线、拟使用的燃油硫含量、燃油设备的燃油消耗率等因素确定。
2.6.6 如脱硫剂会对人员造成伤害,船上进行脱硫剂加注、碱液/浆液制备等可能发生危险的作业时,相关工作人员应使用合适的保护装备(包括大围裙、长袖橡胶手套、抗化学性材料制成的连体工作服、抗化学性材料的贴肉护目镜和/或面罩),保护身体的任何部位免受伤害。船上应至少备有3 套保护装备,这些装备应保存在起居处所外易于到达的专用储存柜内。脱硫剂加注总管及泵附近还应
备有洗眼药水和洗眼器。
2.6.7 脱硫剂储存舱柜及泵不应位于控制站、起居处所和服务处所。脱硫剂储存舱柜及泵所在处所应设有机械通风,通风次数应不小于8 次/h;处所的通道应能从开敞甲板直接进入。脱硫剂储存处所及入口旁,应张贴小心和应急响应有关的安全及操作指示。
2.6.8 采用氢氧化钠(NaOH)溶液(以下简称碱液)做脱硫剂时,还应满足如下要求:
(1) 碱液储存、驳运相关的管系、舱柜、承滴盘或其他可能与溶液接触的任何部件,禁止使用铝、锌、铜或镀锌钢等材料。
(2) 碱液储存及输运过程中应维持在规定温度范围内,为此应设有合适的温度控制措施,防止温度低时发生氢氧化钠结晶,或者温度高时导致材料过度腐蚀。
(3) 储存柜的布置应考虑其他加热舱柜或设施传热产生的影响。当发生溢流或泄漏时,不会滴落到可燃或加热表面。尤其是不能布置在锅炉上方或者与蒸汽管很近。
(4) 储存柜应按钢规第3 篇第3 章第10 节的要求装设空气管、溢流管和液位测量装置。空气管和测量管(如设有)的出口应引至开敞的安全位置,并采取必要措施防止对人员可能造成的伤害。溢出的碱液应引向适合的溢流柜或其他舱柜。
如设置舱柜高液位报警装置替代溢流管,应符合如下要求:
①舱柜设计压力应考虑舱柜底部至空气管出口处液体高度产生的静压力;和②空气管头开口下端应设有合适的碱液承滴盘。
(5) 储存柜应设有就地温度、液位指示装置,并应在有人值班控制站显示。
(6) 可能发生泄露的位置应安装承滴盘,防止泄露的碱液滴落或扩散到其他结构或设备处造成破坏。
(7) 承滴盘应设有泄放装置,将承滴盘内的碱液泄放到溢流柜或其他适合的舱柜,泄放管路上应安装止回阀;或者作为替代,设有泄漏监测装置及快速关闭阀,当发生泄漏时可快速地自动切断碱液,采用该设计布置时,承滴盘的容量应能足够容纳可能的泄露。
(8) 加注站应位于开敞甲板,且远离任何点火源,其布置应保证一旦加注站发生泄漏不会导致碱液与其他非兼容的材料接触或混合。封闭或半封闭的加注站如设有效通风,也可接受。加注接口或其他可能泄露的位置应按2.6.8(6)、(7)的要求设承滴盘。
(9) 如从储存柜引出的管路一旦破坏,会导致碱液逸出,则应在储柜上设有一个快速关闭阀,该阀除能就地关闭外,还应能在储存柜所在处所外易于接近的安全位置进行操作。
2.6.9 如采用氢氧化镁(Mg(OH)2)溶液(以下简称浆液)做脱硫剂,还应根据浆液的特性及危险性,遵循同等安全原则考虑满足2.6.8 的相关要求。
2.7 碱液/浆液制备与供应
2.7.1 采用固体脱硫剂时,应设有必要的碱液/浆液制备系统,将固体脱硫剂配制成一定浓度的碱液/浆液供脱硫装置使用。
2.7.2 碱液/浆液制备系统应设有脱硫剂计量装置,配制的碱液/浆液浓度应满足脱硫系统的要求,并控制在工艺允许的范围内,碱液/浆液的浓度和消耗量宜纳入自动控制系统。
2.7.3 采用氧化镁作为脱硫剂时,制备的浆液细度应至少保证200 目90%的过筛滤,否则应设置预处理系统。
2.7.4 碱液/浆液制备能力应按设计工况下脱硫剂消耗量的150%设计,并应设有足够容量的储罐,容量不低于脱硫系统设计工况下2h 的碱液/浆液消耗量。
2.7.5 应采取合适的措施防止碱液/浆液制备时因放热可能导致的危害。
2.7.6 碱液/浆液储罐应设有防沉淀装置,如加装桨叶式搅拌器、气力/水力搅拌装置等。
2.7.7 应至少设有2 台碱液/浆液供应泵,其中任1 台应能供应脱硫系统设计工况下需要的碱液/浆液,另外1 台备用。
2.7.8 碱液/浆液的供应能自动控制进行,保证系统的脱硫效率持续满足设计要求。
2.7.9 碱液/浆液管系应独立于船上其他管系,且不应设在或通过起居处所、服务处所、控制站。
2.7.10 碱液/浆液管系不应布置在锅炉上方或者靠近蒸汽管路、废气系统、需要绝热的热表面或其他点火源。
2.7.11 碱液/浆液管路的接头应尽量少,除了一些必要的阀及设备采用法兰连接以外,直接连接的管路应全部采用焊接,以尽量减小泄露的风险。
2.7.12 碱液/浆液制备与供应系统中可能发生泄露的位置应安装承滴盘,防止泄露的碱液/浆液滴落或扩散到其他结构或设备处造成破坏。
2.7.13 管系选用的阀及附件应适合工作介质的特性。
2.7.14 碱液/浆液管路上应安装合适的过滤装置,其布置应能保证滤器清洗时,仍能不间断地供应碱液/浆液。
2.7.15 碱液/浆液管系应设有排空及冲洗设施,当脱硫系统停止运行时,及时排空并清洗。